Precision and Passion: Inside the 2025 SkillsUSA Cabinetmaking Championship
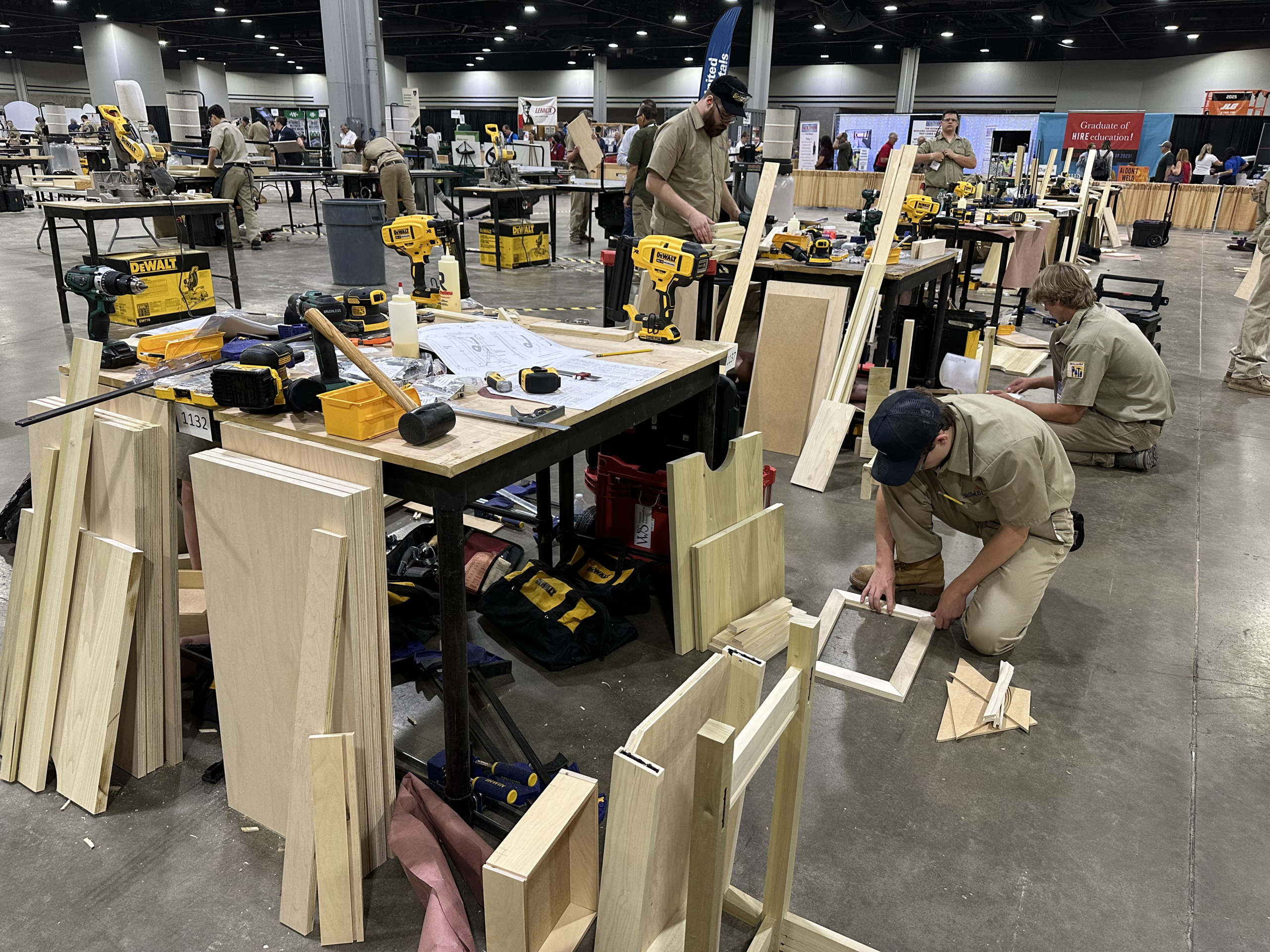
From basic nightstands to intricate Japandi workstations, the SkillsUSA Cabinetmaking Championship continues to push the boundaries of skill and design.
For a quarter of a century, Kent Gilchrist has been a pivotal figure at SkillsUSA, dedicating his time and expertise to shaping the next generation of woodworkers. As the Chair of the SkillsUSA Technical Committee for the National Cabinetmaking Championship for more than a dozen years, his commitment runs deep, stemming from a passion and being a “serial volunteer.” This enduring dedication, he explains, comes from profound personal satisfaction and the joy of working with young people interested in skilled trades and potentially entering the woodworking industry.
The 2025 SkillsUSA Cabinetmaking competition, held from June 23-27 at the Georgia World Congress Center in Atlanta, showcased the impressive talent of high school and postsecondary students from across the nation, including participants from Alaska and Puerto Rico. Out of 16 postsecondary and 40 high school
contestants, the podium finishers demonstrated the highest level of skill and precision.
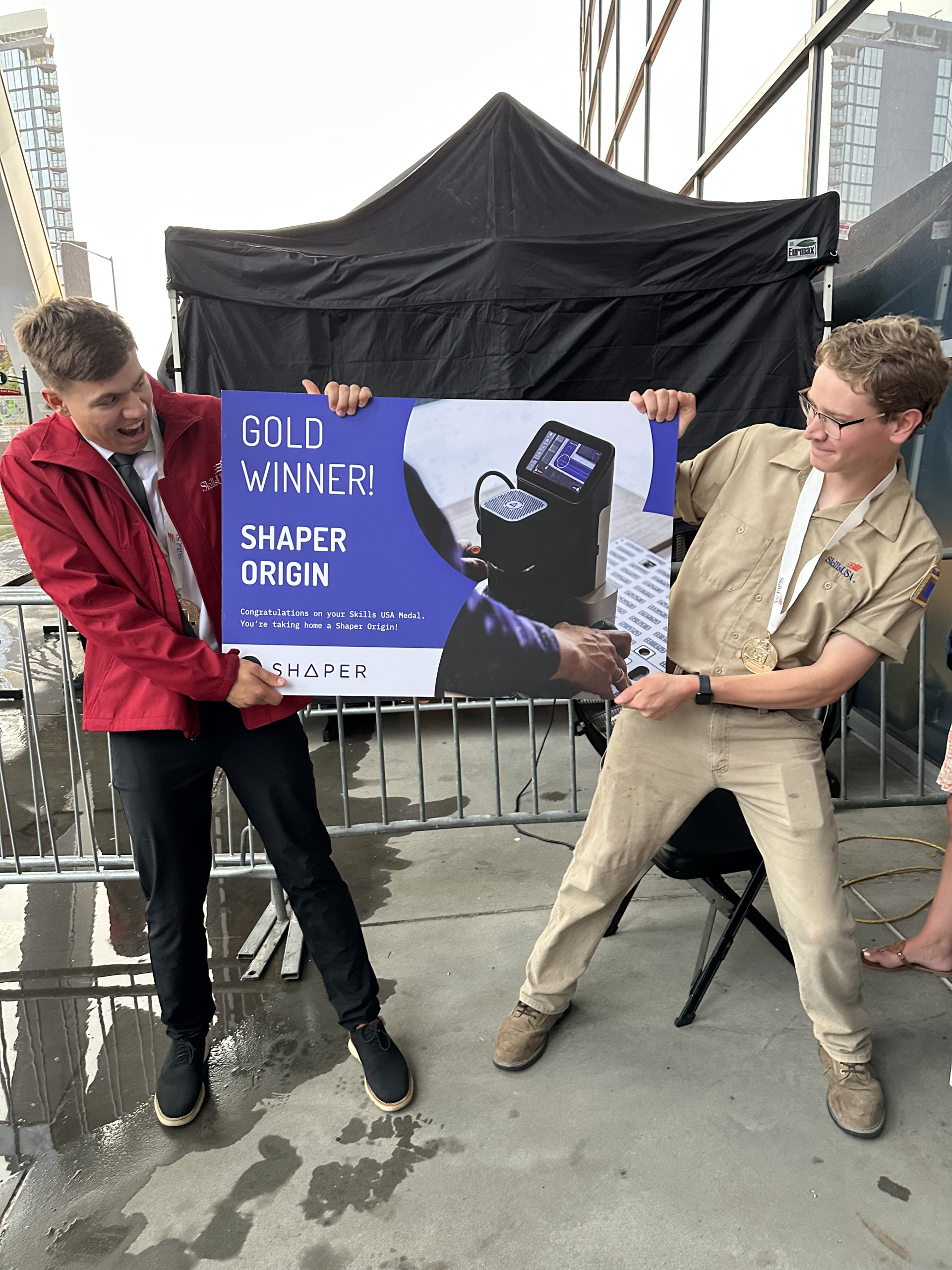
Isaiah Buck, left, and Isaiah Powers won the Gold medals for postsecondary and high school division respectively.
2025 SkillsUSA Cabinetmaking Podium Finishers:
Postsecondary:
- Gold: Isaiah Buck, Northwood Technical College, Rice Lake, WI
- Silver: Nikolaus Brown, Utah Valley University, Orem, UT
- Bronze: Natalia Salt, Metropolitan Community College, Omaha, NE
High School:
- Gold: Isaiah Powers, Fort Wayne Community Schools Academy, Fort Wayne, IN
- Silver: Brody Leerssen, Sheridan High School, Sheridan, WY
- Bronze: Parker Cotton, Monache High School, Porterville, CA
Competitors were tasked with a comprehensive project that demanded a wide array of skills. They were expected to read technical drawings, meticulously lay out parts, create accurate cut lists, and then precisely cut those parts using various tools, including table saws, miter saws, drills, hinge boring machines, and an assortment of hand tools. The final stages involved accurate assembly, sanding, and fine-tuning to meet stringent judge-specified tolerances.
Evolving Craft: From Laminate to Japandi Design
Gilchrist noted that the SkillsUSA Cabinetmaking Competition, which began in 1976, has undergone significant transformations, especially over his 25 years of involvement. He reminisces about the early days when the project was a basic base cabinet – a nightstand with a door, drawer, and countertop, often involving messy laminate work with contact cement.
This year’s project, however, was a testament to the evolution of design and technique: a Japandi style workstation made predominantly with maple plywood. This unique blend of Japanese and Scandinavian design, conceived by Gilchrist and a friend with Korean heritage, was envisioned as a “station where you can do some chopping and meal prep.” The workstation featured “a little bit of storage,” including a cabinet that proved to be the most challenging aspect of the design for the contestants.
The door itself was a masterpiece of complexity, featuring three separate panels within a stile and rail construction. One of these, a quarter-inch panel, included what Gilchrist called the “Zen Garden design,” a scroll machined with precision using a Shaper Origin after initial cuts on a Grizzly bandsaw.
“We designed the project in relation to what industry is looking for,” Gilchrist explained. “The key elements are consistent with what we have done in the past. We are always looking for skills in measuring and layout, material optimization, and understanding the sequence of events that have to take place to build the project. In addition to measuring and layout, we continue to lean heavily on machine skills. All of those elements are directly related to WCA’s mission and credentialing programs.”
The Cut List Challenge
Gilchrist pointed out a significant hurdle for many contestants: mistakes on their cut lists. “A number of competitors didn’t do well calculating parts for their cut lists. Possibly they haven’t had the necessary training,” Gilchrist added. “We only had one perfect score on the cut lists, and then we had some that just had so many wrong answers.”
The cut lists were created during orientation, the pre-day meeting where Gilchrist leads an exercise in sequencing and process understanding, providing crucial guidance without giving away all the answers. This year’s orientation also included a new hands-on element. “One thing we did different during orientation this year is that we had them glue-up a 1-inch solid wood top that they milled the next day,” Gilchrist said. “They did the glue-up during orientation after they visited each station and reviewed the project.” Students had 8 hours of fabrication and assembly time on the actual competition day.
Intricate Design and Technical Demands
Gilchrist highlighted several fabrication challenges in this year’s design:
- Angled Components: The cabinet was built with an end panel on a 5-degree angle, requiring the door and drawer front to precisely match this angle. Understanding the interaction of these angles, particularly with the muttin bars (which were a quarter-inch longer with a tenon for a groove fit), was crucial.
- Zen Garden Feature: The intricate scroll machined on the door with Shaper Origin hand-held CNC router demanded precision and careful execution.
- Dadoes and Joinery: The left-side panel featured dadoes also on a 5-degree angle, requiring contestants to account for depth. The right-side panel, legs, and rails, assembled using the Lamello Zeta system, added another layer of complexity.
Contestants utilized a variety of tools and prepared materials, including an SCM edgebander and SawStop table saws for dadoes and solid wood parts. They received pre-grooved door stiles, rails, and muttin bars, with materials planed to thickness and size. Beyond technical skill, time management and keeping a cool head were key elements for success.
“The hardest part was the door,” Gilchrist said. “When we revealed the project during orientation, there was a gasp. I heard one of the contestants say, ‘At state, we just built a box.'” He emphasized that SkillsUSA projects have not been simple for the past decade, and past drawings are available for those who do their research.
The angled dadoes on the 5-degree angled cabinet added another layer of difficulty, even with the angles provided.
Fewer Repeat Contestants and Unwavering Spirit
A notable difference this year was the lower number of repeat contestants, with only about 15-20% returning compared to 40-50% last year. While repeaters had an advantage in knowing the types of challenges to expect, all competitors, regardless of their struggles, were encouraged to continue even though they may not have a completed project.
“We always have contestants that really struggle, and we did this year as well. Overall, they were positive. Nobody got mad and frustrated to the point that they wanted to leave,” Gilchrist affirmed. “They were very gracious and thankful that we are doing this. If someone is struggling, we’re going to help them a little bit. The competitors stay and they work through something – build something even if they don’t take it home. We end up with some creative projects as well.”
This unwavering commitment to seeing projects through underscores the positive and supportive environment fostered at SkillsUSA. Gilchrist also noted the practical aspirations of the participants.
“Clearly kids are still interested in getting into the skilled trade,” he said. “A number of these kids in the top five are actually working in cabinet shops. The winner of high school division is working full time in a cabinet shop right now. I noted that some others are working in shops. Others want to work in shops or even start their own.”
Prizes and Industry Support
The prizes for the top performers were substantial, reflecting the strong industry support for SkillsUSA:
- First Place: Grizzly 14-inch bandsaw, SawStop compact saw, Shaper Origin handheld CNC router.
- Second Place: Grizzly track saw, DeWalt five-piece cordless tool kit, Richelieu — Bosch trim routers.
- Third Place: Grizzly drill bit set, Richelieu pin nailer, and random orbit sander.
Beyond individual prizes, schools of the Gold medalists received a Lamello ZETA system from Colonial Saw, and Gold schools also received a benchtop pocket hole machine from Castle Tool. Every competitor received a DeWalt 28-piece drill/driver attachments tool kit. Furthermore, DeWalt donated 60 cordless sanders and four new 12-inch slide compound miter saws to SkillsUSA, further equipping future SkillsUSA National Cabinetmaking Championships.
The SkillsUSA Championships is the premier showcase of America’s most highly skilled career and technical education students and one of the largest hands-on workforce development events in the world. Held in conjunction with SkillsUSA’s National Leadership & Skills Conference each year, this awe-inspiring event features more than 6,500 state champions from across the United States competing head-to-head in 114 skilled and leadership competitions. Covering over 1.79 million square feet of floor space at the Georgia World Congress Center – equivalent to 31 football fields – the philosophy of the SkillsUSA Championships is to reward students for excellence, to involve industry in directly evaluating student performance, and to keep classroom training relevant to employers’ needs.